A indústria brasileira está passando por uma transformação digital sem precedentes, impulsionada pela adoção de sistemas ciber-físicos. Esses sistemas integram tecnologias avançadas, como sensores, dispositivos conectados, análise de dados em tempo real e inteligência artificial, para criar fábricas mais eficientes, flexíveis e inovadoras. Neste artigo, exploraremos como esses sistemas ciber-físicos estão revolucionando a manufatura no Brasil, possibilitando a criação de ambientes de produção inteligentes e preparados para os desafios da Indústria 4.0.
Principais Aprendizados
- Entender o conceito de sistemas ciber-físicos e sua importância na Indústria 4.0
- Conhecer os principais componentes da manufatura integrada por computador
- Explorar o papel da Internet das Coisas Industrial e da análise de Big Data na transformação das fábricas
- Compreender como a Computação em Nuvem e a Inteligência Artificial impulsionam a inteligência das fábricas
- Reconhecer os desafios da cibersegurança industrial e as estratégias de mitigação
O que são sistemas ciber-físicos?
Os sistemas ciber-físicos são a integração de processos físicos e computacionais, combinando sensores, atuadores, sistemas de computação e comunicação. Eles desempenham um papel fundamental na Indústria 4.0, permitindo a automação, a coleta de dados em tempo real e a tomada de decisões inteligentes nas fábricas.
Definição e conceitos básicos
Sistemas ciber-físicos são sistemas que integram o mundo físico e o mundo virtual, permitindo a Internet das Coisas Industrial e a integração de sistemas. Eles combinam elementos de computação, comunicação e controle para monitorar e gerenciar processos físicos, criando uma sinergia entre o digital e o real.
Importância na Indústria 4.0
Na Indústria 4.0, os sistemas ciber-físicos desempenham um papel crucial ao permitir a automação avançada, a coleta de dados em tempo real e a tomada de decisões baseada em informações precisas. Essa integração entre o mundo físico e o digital é essencial para o desenvolvimento de fábricas inteligentes e a otimização dos processos de manufatura.
Características dos Sistemas Ciber-Físicos | Benefícios na Indústria 4.0 |
---|---|
Integração entre o físico e o digital | Maior eficiência operacional |
Coleta e análise de dados em tempo real | Tomada de decisões mais informadas |
Capacidade de monitoramento e controle remoto | Maior flexibilidade e agilidade na produção |
Automação avançada de processos | Redução de custos e desperdícios |
Sistemas de Manufatura Integrados por Computador
Os Sistemas de Manufatura Integrados por Computador (CIM) desempenham um papel fundamental na transformação das fábricas em ambientes inteligentes. Essa tecnologia integra diferentes componentes, como robótica, automação industrial e sistemas de planejamento de recursos empresariais, para otimizar os processos de produção.
A integração desses sistemas permite uma eficiência operacional aprimorada, oferecendo maior flexibilidade, qualidade e produtividade na manufatura. Ao unificar os fluxos de informação e controle, os sistemas CIM possibilitam uma visão holística da cadeia de produção, facilitando a tomada de decisões estratégicas.
Algumas das principais características e benefícios dos sistemas CIM incluem:
- Integração de diferentes tecnologias, como robótica, controle numérico computadorizado e sistemas de planejamento de recursos empresariais.
- Automação e otimização dos processos de fabricação, reduzindo erros e aumentando a produtividade.
- Maior flexibilidade na produção, permitindo adaptações rápidas a mudanças na demanda e no mercado.
- Melhoria na qualidade dos produtos, por meio de processos de fabricação mais precisos e controlados.
- Coleta e análise de dados em tempo real, possibilitando a tomada de decisões informadas.
Ao adotar os Sistemas de Manufatura Integrados por Computador, as empresas podem alcançar uma eficiência operacional significativa, respondendo de forma ágil às exigências do mercado e garantindo sua competitividade no cenário da Indústria 4.0.
Tecnologia | Benefício |
---|---|
Robótica | Automação de tarefas repetitivas e precisas, aumentando a produtividade. |
Controle Numérico Computadorizado (CNC) | Maior precisão e qualidade na fabricação de peças e componentes. |
Sistemas de Planejamento de Recursos Empresariais (ERP) | Integração de informações e processos em toda a organização, permitindo uma visão holística da produção. |
Internet das Coisas Industrial
A Internet das Coisas Industrial (IIoT) está transformando a maneira como as empresas manufatureiras operam. Essa tecnologia conecta sensores e dispositivos em toda a linha de produção, coletando dados em tempo real sobre os processos e o desempenho da fábrica.
Sensores e dispositivos conectados
Os sensores industriais monitoram diversos aspectos da produção, como temperatura, pressão, vibração, fluxo, entre outros. Esses dados são transmitidos por meio de redes de comunicação, como Wi-Fi, Bluetooth ou 5G, permitindo o acompanhamento contínuo dos processos.
Coleta e análise de dados em tempo real
Com a coleta de dados em tempo real, os gerentes e engenheiros podem tomar decisões mais informadas, ajustando a produção de acordo com as necessidades e identificando oportunidades de otimização. A análise de dados avançada, combinada com a inteligência artificial, também auxilia na detecção precoce de problemas e na manutenção preditiva dos equipamentos.
Benefícios da IIoT | Percentual de melhoria |
---|---|
Eficiência operacional | 18% |
Produtividade | 15% |
Qualidade do produto | 12% |
Segurança | 10% |
A Internet das Coisas Industrial está no cerne da Indústria 4.0, permitindo a integração entre sistemas físicos e digitais para aprimorar a eficiência, a qualidade e a flexibilidade da manufatura.
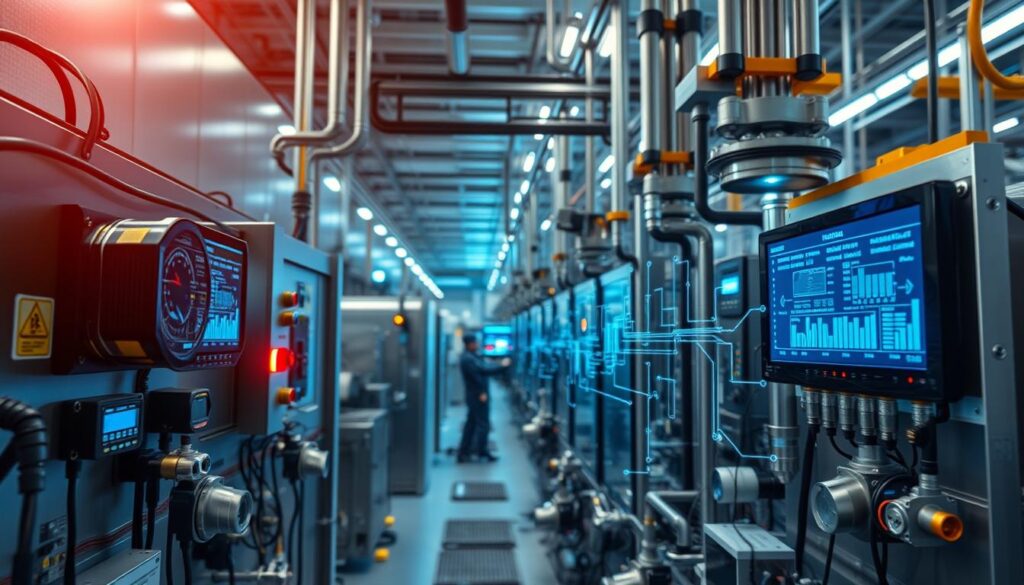
“A IIoT é essencial para as fábricas se tornarem mais inteligentes, ágeis e competitivas no mercado global.”
Big Data Industrial
O Big Data Industrial representa uma revolução na forma como as empresas abordam a coleta, armazenamento e análise de dados em ambientes de manufatura. Essa abordagem permite que as organizações identifiquem padrões ocultos, prevejam problemas e tomem decisões mais embasadas, resultando em melhorias significativas na eficiência e produtividade de suas operações.
A implementação do Big Data Industrial envolve a utilização de sensores e dispositivos conectados que geram uma enorme quantidade de dados sobre os processos de produção. Esses dados são então armazenados e processados por meio de poderosas ferramentas de análise, capazes de identificar insights valiosos que não seriam evidentes em uma análise manual tradicional.
- Otimização de processos: O Big Data Industrial permite que as empresas identifiquem gargalos e oportunidades de melhoria em seus processos de fabricação, otimizando a eficiência e reduzindo desperdícios.
- Prevenção de falhas: Ao analisar padrões e tendências nos dados, as organizações podem antecipar problemas potenciais em máquinas e equipamentos, implementando ações preventivas antes que ocorram falhas.
- Tomada de decisão embasada: Com base nos insights gerados pelo Big Data Industrial, as empresas podem tomar decisões mais informadas sobre investimentos, planejamento da produção e estratégias de negócios.
À medida que as empresas adotam o Big Data Industrial em seus ambientes de manufatura, elas se aproximam cada vez mais da realidade da Indústria 4.0, na qual os sistemas ciber-físicos e a Análise de dados desempenham um papel fundamental para alcançar a Tomada de decisão mais precisa e ágil.
Computação em Nuvem Industrial
A Computação em Nuvem Industrial tem se destacado como uma solução atraente para as empresas que buscam modernizar sua infraestrutura de TI. Essa abordagem oferece acesso remoto a recursos computacionais, como armazenamento e processamento, sem a necessidade de investir em uma infraestrutura local robusta.
Vantagens da Computação em Nuvem Industrial
Uma das principais vantagens da Computação em Nuvem Industrial é a escalabilidade. As empresas podem ajustar rapidamente seus recursos de TI de acordo com as demandas flutuantes da produção, evitando investimentos excessivos em infraestrutura própria. Além disso, a Computação em Nuvem Industrial também pode reduzir os custos operacionais, uma vez que a manutenção e o gerenciamento da infraestrutura ficam a cargo do provedor de serviços.
Desafios da Computação em Nuvem Industrial
No entanto, a adoção da Computação em Nuvem Industrial também enfrenta alguns desafios, principalmente relacionados à segurança e privacidade dos dados industriais. Empresas do setor manufatureiro lidam com informações confidenciais e sensíveis, e é essencial garantir a proteção desses dados durante a transferência e o armazenamento na nuvem. Portanto, a Segurança de dados é um fator crucial a ser considerado na implementação da Computação em Nuvem Industrial.
Vantagens | Desafios |
---|---|
Escalabilidade | Segurança de dados |
Redução de custos | Privacidade dos dados |
Acesso remoto a recursos de TI | Conformidade regulatória |
Ao adotar a Computação em Nuvem Industrial, as empresas devem equilibrar os benefícios com os desafios de segurança e privacidade, a fim de aproveitar plenamente as vantagens dessa tecnologia e proteger seus dados críticos.
Transformando fábricas em ambientes inteligentes com sistemas ciber-físicos
As fábricas inteligentes estão se tornando uma realidade graças à adoção de sistemas ciber-físicos na manufatura avançada. Esses sistemas permitem uma integração mais eficiente entre máquinas, processos e recursos humanos, otimizando a produção e reduzindo erros e desperdícios.
Uma das principais características dos sistemas ciber-físicos é a capacidade de coletar e analisar dados em tempo real. Isso possibilita a tomada de decisões mais ágeis e assertivas, melhorando a eficiência geral da fábrica.
Outra vantagem é a possibilidade de automatizar tarefas repetitivas e monitorar o desempenho dos equipamentos de forma contínua. Isso permite que os profissionais de produção se concentrem em atividades de maior valor agregado, como a solução de problemas e a implementação de melhorias no processo.
Recursos | Benefícios |
---|---|
Integração de máquinas, processos e pessoas | Otimização da produção e redução de erros e desperdícios |
Coleta e análise de dados em tempo real | Tomada de decisões mais ágeis e assertivas |
Automação de tarefas repetitivas | Liberação de profissionais para atividades de maior valor agregado |
A integração de sistemas ciber-físicos é um passo fundamental para a transformação das fábricas em ambientes inteligentes, capazes de responder de forma ágil às demandas do mercado e conquistar vantagens competitivas.
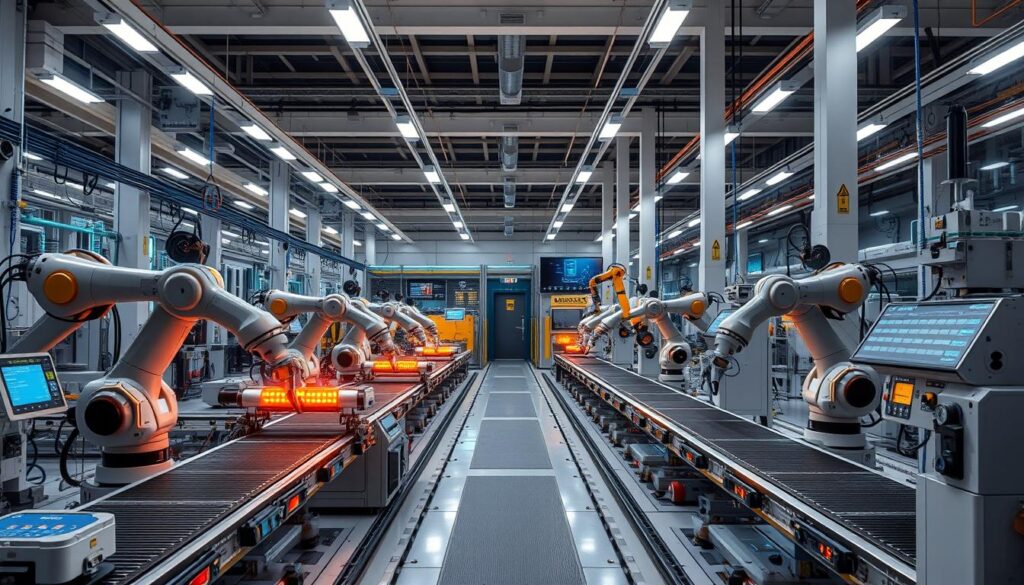
Inteligência Artificial na Manufatura
A Inteligência Artificial (IA) está transformando a indústria de manufatura, tornando-a mais eficiente e competitiva. Empresas líderes estão implementando soluções de IA para automatizar tarefas, melhorar a qualidade dos produtos, realizar manutenção preditiva de máquinas e otimizar os processos de produção.
Aplicações e casos de uso
A IA está sendo aplicada na manufatura de diversas formas, trazendo benefícios significativos:
- Automação de tarefas: Sistemas de IA podem realizar tarefas repetitivas e monótonas, aumentando a produtividade e a eficiência.
- Controle de qualidade: Algoritmos de IA podem detectar defeitos e problemas de qualidade em produtos, permitindo a correção imediata.
- Manutenção preditiva: A IA analisa dados de sensores para prever a necessidade de manutenção de máquinas, evitando paradas não programadas.
- Otimização de processos: Sistemas de IA podem identificar gargalos, otimizar rotas de transporte e ajustar parâmetros de produção, aumentando a produtividade e reduzindo custos.
Empresas líderes, como a Siemens e a GE, já implementaram soluções de IA em suas linhas de produção, obtendo resultados expressivos em termos de eficiência, qualidade e redução de custos.
“A Inteligência Artificial está impulsionando a próxima geração da indústria manufatureira, tornando-a mais inteligente, ágil e competitiva.”
Cibersegurança Industrial
À medida que as indústrias se transformam em ambientes inteligentes e interconectados, a cibersegurança industrial se torna uma prioridade crucial. Com a adoção crescente de sistemas ciber-físicos, Internet das Coisas Industrial e outras tecnologias avançadas, as empresas enfrentam uma nova gama de riscos cibernéticos que precisam ser abordados de maneira eficaz.
Alguns dos principais riscos cibernéticos que as fábricas inteligentes enfrentam incluem:
- Ataques de ransomware que podem paralisar as operações
- Invasão de sistemas de controle e automação industrial
- Interceptação e manipulação de dados industriais sensíveis
- Interrupção da cadeia de suprimentos e da continuidade das operações
Para mitigar esses riscos cibernéticos, as empresas precisam adotar uma abordagem abrangente de cibersegurança industrial, incluindo:
- Implementação de soluções de proteção de dados robustas, como criptografia e backup de dados
- Treinamento e conscientização contínua da equipe sobre boas práticas de cibersegurança
- Adoção de sistemas de detecção e resposta a incidentes cibernéticos
- Realização de testes de penetração e avaliações regulares de vulnerabilidades
- Implementação de controles de acesso e autenticação rigorosos em todos os sistemas
Ao investir em cibersegurança industrial, as empresas podem proteger seus ativos, garantir a continuidade das operações e aproveitar os benefícios das fábricas inteligentes com confiança.
Risco Cibernético | Impacto Potencial | Estratégia de Mitigação |
---|---|---|
Ataques de ransomware | Paralisação das operações, perda de dados | Backup e criptografia de dados, detecção e resposta a incidentes |
Invasão de sistemas de automação industrial | Interrupção da produção, danos a equipamentos | Controle de acesso, segmentação de rede, testes de penetração |
Vazamento de dados industriais confidenciais | Perda de propriedade intelectual, danos à reputação | Classificação e proteção de dados, controles de acesso |
Conclusão
Os sistemas ciber-físicos desempenham um papel fundamental na transformação das fábricas em ambientes inteligentes, impulsionando a Transformação digital e a Indústria 4.0 no Brasil. Com a integração de tecnologias como Internet das Coisas, Big Data, Inteligência Artificial e Computação em Nuvem, as empresas podem otimizar seus processos, reduzir custos e se tornarem mais competitivas no mercado.
Essa Manufatura inteligente permite que as fábricas se tornem mais eficientes, produtivas e inovadoras, aproveitando ao máximo os Sistemas ciber-físicos e suas capacidades de coleta e análise de dados em tempo real. Essa integração entre sistemas físicos e digitais é fundamental para impulsionar a competitividade da indústria brasileira no cenário global.
Portanto, a adoção de Sistemas ciber-físicos se apresenta como uma estratégia essencial para as empresas que desejam se manter à frente em um mercado cada vez mais dinâmico e exigente. Essa transformação digital é um caminho sem volta para a indústria, e as organizações que a abraçarem com agilidade e visão estratégica terão uma vantagem competitiva significativa.
FAQ
O que são sistemas ciber-físicos?
Sistemas ciber-físicos são a integração de processos físicos e computacionais, combinando sensores, atuadores, sistemas de computação e comunicação. Eles desempenham um papel fundamental na Indústria 4.0, permitindo a automação, a coleta de dados em tempo real e a tomada de decisões inteligentes nas fábricas.
Qual a importância dos sistemas ciber-físicos na Indústria 4.0?
Os sistemas ciber-físicos são a base da Indústria 4.0, pois permitem a integração entre o mundo físico e o digital, possibilitando a automação, a coleta de dados em tempo real e a tomada de decisões inteligentes nas fábricas.
O que são os Sistemas de Manufatura Integrados por Computador (CIM)?
Os Sistemas de Manufatura Integrados por Computador (CIM) integram diferentes tecnologias, como robótica, controle numérico computadorizado e sistemas de planejamento de recursos empresariais, para otimizar os processos de produção. Essa integração permite maior eficiência, flexibilidade e qualidade na manufatura.
O que é a Internet das Coisas Industrial (IIoT)?
A Internet das Coisas Industrial (IIoT) conecta sensores e dispositivos em toda a linha de produção, coletando dados em tempo real. Essa conectividade permite monitoramento, controle e otimização dos processos, com base na análise de grandes volumes de dados.
O que é Big Data Industrial?
Big Data Industrial refere-se à coleta, armazenamento e análise de grandes volumes de dados gerados pelos sistemas de manufatura. Essa abordagem permite que as empresas identifiquem padrões, prevejam falhas e tomem decisões mais embasadas, melhorando a eficiência e a produtividade.
Quais as vantagens e desafios da Computação em Nuvem Industrial?
A Computação em Nuvem Industrial oferece acesso remoto a recursos de TI, como armazenamento e processamento, sem a necessidade de investir em infraestrutura local. Isso traz vantagens, como escalabilidade e redução de custos, mas também desafios relacionados à segurança e privacidade dos dados industriais.
Como a Inteligência Artificial está sendo aplicada na manufatura?
A Inteligência Artificial está sendo aplicada na manufatura para automatizar tarefas, melhorar a qualidade dos produtos, realizar manutenção preditiva de máquinas e otimizar os processos de produção. Empresas líderes estão implementando soluções de IA para aumentar a eficiência e a competitividade.
Quais os principais riscos de cibersegurança industrial e como mitigá-los?
À medida que as fábricas se tornam mais conectadas e dependentes de sistemas digitais, a cibersegurança se torna um desafio crítico. As empresas precisam adotar estratégias eficazes de proteção contra ameaças cibernéticas, como ataques de ransomware e invasões de sistemas, para salvaguardar seus ativos e a continuidade das operações.